Beam brings Rovco and Vaarst back together for undersea robotics
Bristol hosts one of the world’s leading developers of undersea systems, which is bringing its two separate companies together under Beam Global.
Underwater robotic system developer Rovco spun out its R&D division into a separate company called Vaarst in 2021 with 29 staff.
The two companies have been brought back together in a company called Beam to focus on the market for developing, building and maintaining off shore wind turbines with remotely operated robots.
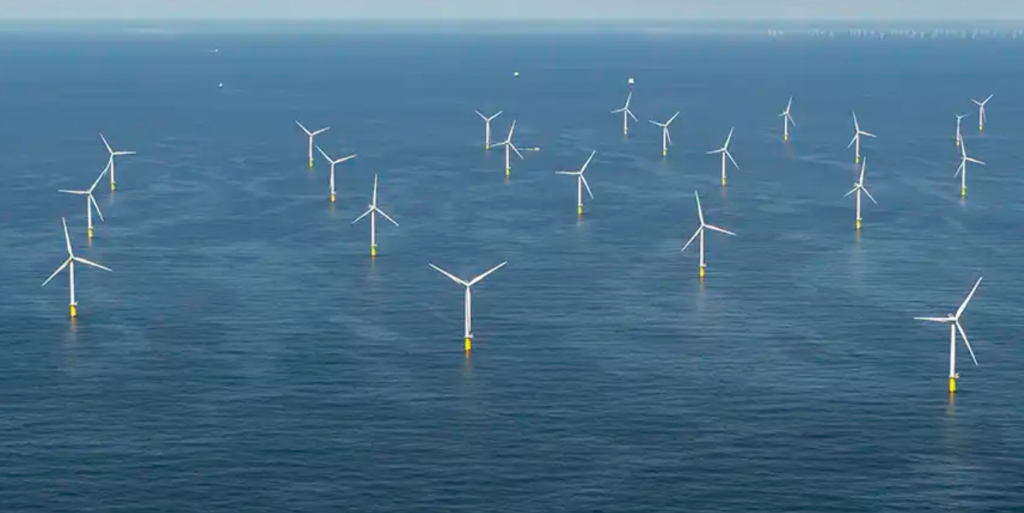
Rovco has developed an AI system that dramatically accelerates the identification and clearance of unexploded ordnance (UXO) in the North Sea. Historically, this process could take up to two and a half years, with marine surveyors meticulously analysing seabed surveys. Today with the Vaarst AI-driven technology, this timeline has been reduced to just two-to-three months. But the impact of AI goes far beyond UXO clearance.
This also helps with a broader issue facing the offshore renewables and tech industry: a looming skills shortage. “We foresee a skills shortage in offshore renewables,” said Joe Tidball, co-founder of Rovco. “So how do we take the number of people we have right now and allow them to do more work? It comes back to AI, allowing computers to look through multiple data sets at one time.”
This AI technology allows for more efficient processing and analysis of large volumes of data, enabling teams to accomplish more with the same resources. By leveraging AI, Rovco is not just speeding up specific tasks; we are redefining how the entire offshore wind sector operates, ensuring that the industry can scale effectively to meet future demands.
“We need to see significant technology advancements that cut costs, shorten project time and improve processes across the entire lifecycle of offshore wind farms if we are to come close to meeting global goals. Whether its surveys for site preparation, critical undersea operational projects, or oil field decommissioning, our combination of AI, rich data and robotics is transforming what’s possible in offshore wind by automating and accelerating processes, bringing immediate time and cost savings,” said Beam.
“Autonomous robotics are the key to reducing the cost of offshore operations. At the same time, digitalisation of field assets is essential as the industry evolves, marrying these two concepts is needed to realise the real benefit of modern tech. It’s the data that has to drive the vehicles. Vaarst is committed to unlocking the potential of offshore robotics for all,” said Vaarst CEO and Founder, Brian Allen.
Cutting-edge technologies are also a key solution to one of the industry’s most pressing challenges: the workforce shortage. An engineer partnered with artificial intelligence completes exponentially more work than they can alone. Unsupervised autonomy transforms the role of the driver of one vehicle into the caretaker of an autonomous fleet. AI brings first power closer, shifts sea-based jobs to homes and offices, and improves the efficiency of offshore workers and marine assets says Beam.
Digital twin for Temple Meads station
A SouthWest startup has developed a digital twin virtual version of Temple Meads to manage sensors across the Bristol station.
The digital twin technology is supplied by start-up Optimise AI and installed at Bristol Temple Meads as part of the Station Innovation Zone testbed. The sensors across the station have helped to inform rail managers of efficiency savings that could be found both inside and around the historic building.
The digital twin has a 3D visualisation of the station and takes in data from sensors across the site. This has shown that electricity consumption at Temple Meads has the potential to be reduced by as much as a third from static measures (such as new windows, doors, better insulation, heat pumps or LED lighting) or with dynamic approaches such as changing heating levels or intensity of illumination.
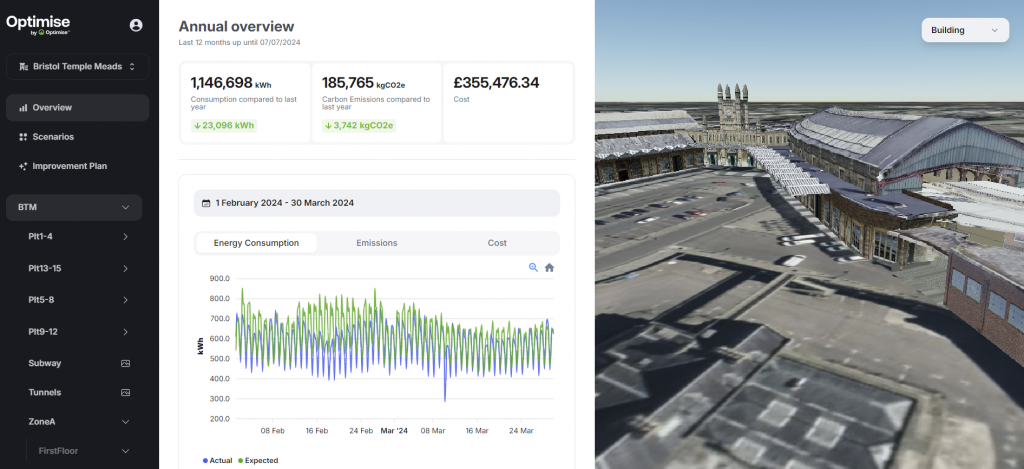
“We created a digital twin to generate a virtual representation of Bristol Temple Meads in order to work out exactly what is keeping the station functioning, and keeping its occupants happy and healthy. With all of that information, we can generate a scenario for improvement,” said Optimise AI director Nick Tune. He is an engineering technologist who previously worked for the Building Research Establishment (BRE) in Wales and consultant Atkins. He established Optimise AI at the start of this year as a spin out from Cardiff University’s school of engineering.
Sensors around the station measure how many people were using rooms and public spaces in order to determine the most appropriate temperature and lighting levels, and to monitor humidity and carbon dioxide around the station.
It also used sensors at barrier gates and considered train timetable detail, to help the system learn which platforms were about to receive an influx of passengers when, in order to alter energy output accordingly and save money.
In stations, the largest consumers of energy tend to be lighting and the operation of machinery such as lifts and escalators. “Stations can be massively wasteful environments and there is often a lack of knowledge as to how many of them are performing,” says Tune.
“My whole focus is around using digital systems to deliver a more sustainable built environment by minimising electricity usage and carbon emissions. We have shown the system can deliver savings, having previously used the technology in care homes and leisure centres.
“What we have created here is a digital twin that provides real value using live data to predict how a station is going to perform, and how conditions can be improved.”
Moving forward, Tune hopes to roll out the digital twin to other large stations, as well as rail depots and line-side buildings housing operational equipment beside railway tracks. “There’s a massive opportunity to look energy and carbon for the railways on a whole estate level,” he said.